Modern Plastic Manufacturing
The world of plastic manufacturing has evolved significantly over the past few decades. Today, two prominent techniques dominate the industry—Mould Injection Moulding and Thermoformed Products. These processes have revolutionized how we create everything from medical devices to automotive parts and consumer packaging. The demand for efficient, reliable, and cost-effective plastic forming methods has never been higher, and businesses are constantly looking for ways to improve their production strategies.
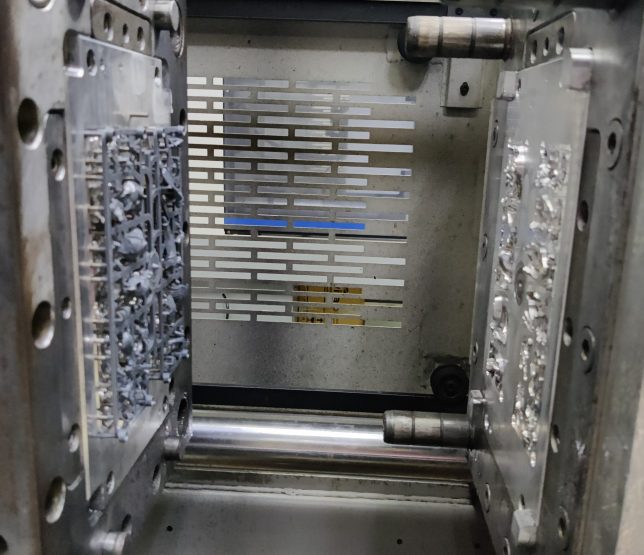
Understanding Mould Injection Moulding
Mould Injection Moulding is one of the most popular plastic manufacturing methods used in high-volume production. It involves injecting molten plastic material into a precisely designed mould, where it cools and solidifies into the desired shape. This process is ideal for creating complex parts with tight tolerances and consistent quality.
The benefits of Mould Injection Moulding are numerous. It provides excellent dimensional accuracy, minimal material waste, and fast production cycles. It’s suitable for a wide range of plastics, including thermoplastics and thermosets. Industries such as automotive, electronics, and medical rely heavily on this technique for producing robust and intricate parts.
Thermoformed Products and Their Applications
On the other side of the plastic forming spectrum are Thermoformed Products. Thermoforming is a manufacturing process where a plastic sheet is heated until pliable, then shaped using a mould and trimmed to create a usable product. Unlike Mould Injection Moulding, which creates more complex and thick-walled parts, thermoforming is often used for simpler, thin-walled items.
Common applications of Thermoformed Products include food packaging, trays, clamshell containers, and disposable cups. Thermoforming is generally more cost-effective for short production runs and prototypes. The tooling costs are lower, and the turnaround time is typically quicker compared to injection moulding.
Comparing Both Methods
While both Mould Injection Moulding and Thermoformed Products play critical roles in the plastic manufacturing industry, they are suited for different needs. Injection moulding is best for high-volume, high-precision applications that require strong mechanical properties. It offers excellent repeatability and a smooth surface finish, making it suitable for final-use parts.
Thermoforming, however, is more adaptable for lightweight and large parts with lower tooling costs. It is less expensive to set up and is particularly effective for large-area items that do not require intricate details. The choice between the two often comes down to the product’s design, volume, and cost considerations.
Innovation and Sustainability
As industries push for sustainable manufacturing solutions, both techniques are being refined for environmental efficiency. Recyclable and biodegradable plastics are being integrated into both Mould Injection Moulding and Thermoformed Products. Energy-efficient equipment and closed-loop recycling systems are also becoming standard in many manufacturing plants.
Modern developments in design software, robotics, and automation further enhance the efficiency and accuracy of these manufacturing processes. Companies are now able to produce custom parts at a faster pace while maintaining superior quality standards and reducing material waste.
Why Expertise Matters
Working with a knowledgeable and experienced plastic manufacturing partner is crucial to achieving the desired product outcomes. An expert can guide businesses through the material selection process, tooling design, and production optimization. They can also help balance cost, performance, and time-to-market in a competitive manufacturing environment.
Both Mould Injection Moulding and Thermoformed Products offer unique advantages in plastic manufacturing. Choosing the right method depends on your specific application, design complexity, and production volume. For tailored plastic solutions that combine innovation, precision, and efficiency, partnering with a trusted provider is essential.